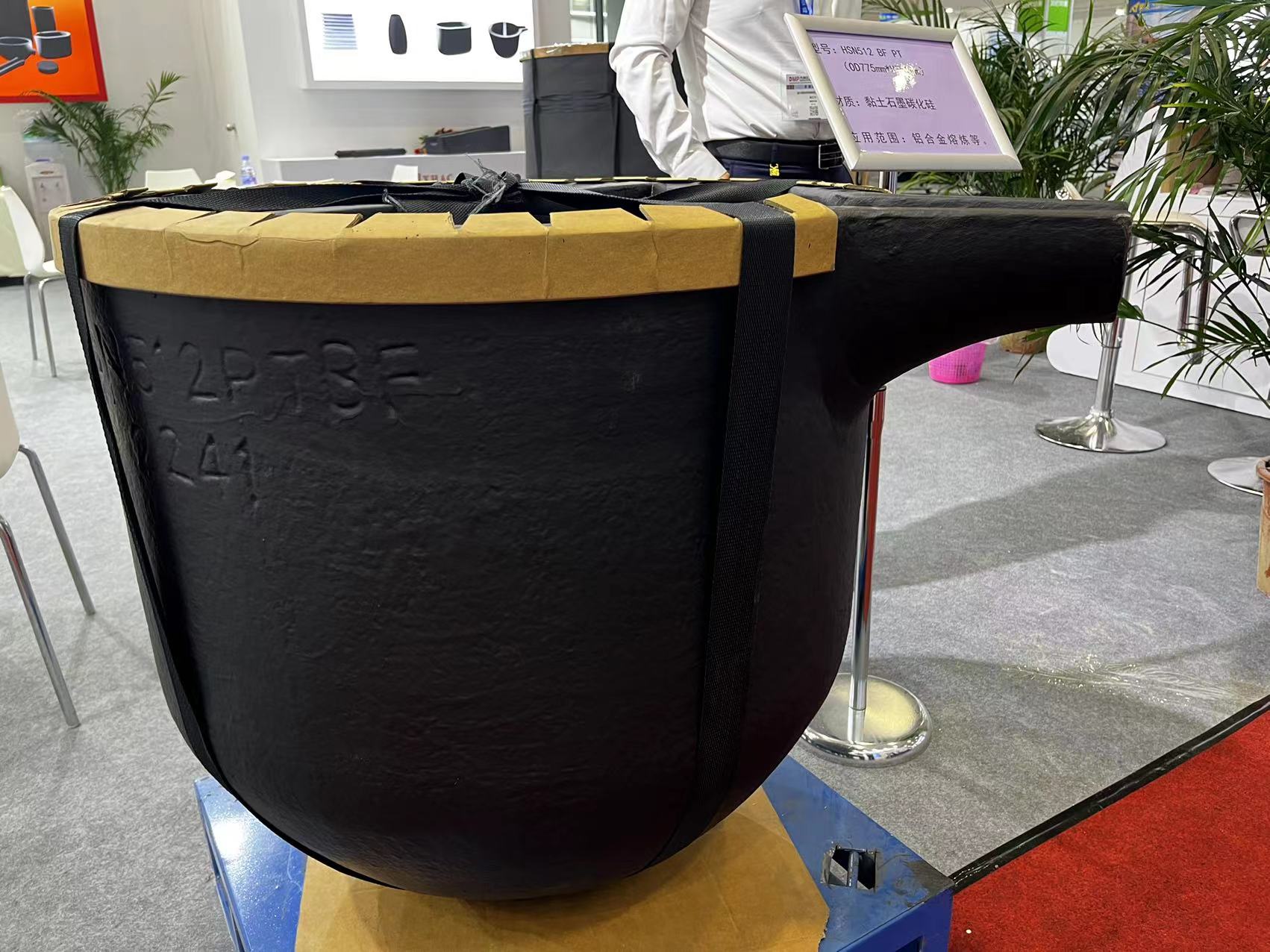
Die voorbereidingsmetode van hoë sterkteGrafiet silikonkarbied smeltkroesVir metaalsmelting bevat die volgende stappe: 1) voorbereiding op grondstowwe; 2) primêre vermenging; 3) materiaaldroging; 4) verplettering en sifting; 5) Sekondêre materiaalvoorbereiding; 6) sekondêre vermenging; 7) druk en vorm; 8) sny en snoei; 9) droog; 10) beglazing; 11) primêre skietery; 12) impregnering; 13) sekondêre skietery; 14) deklaag; 15) Voltooi produk. Die smeltkroes wat met behulp van hierdie nuwe formule en produksieproses geproduseer word, het 'n sterk weerstand teen hoë temperatuur en weerstand teen korrosie. Die gemiddelde leeftyd van die smeltkroes bereik 7-8 maande, met 'n eenvormige en defekvrye interne struktuur, hoë sterkte, dun mure en goeie termiese geleidingsvermoë. Daarbenewens verbeter die glaslaag en deklaag op die oppervlak, tesame met veelvuldige droog- en skietprosesse, die korrosiebestandheid van die produk aansienlik en verminder die energieverbruik met ongeveer 30%, met 'n hoë mate van vergoeding.
Hierdie metode behels die veld van nie-ysterhoudende metallurgie-giet, veral die voorbereidingsmetode van hoë-sterkte grafiet-silikonkarbied-smeltkroes vir metaalsmelting.
[Agtergrondtegnologie] Spesiale grafiet-silikonkarbied-kruispunte word hoofsaaklik gebruik in nie-ysterhoudende metaalgiet- en smeeprosesse, sowel as in die herstel en verfyning van edelmetale, en die produksie van hoë temperatuur en korrosie-weerstandige produkte wat benodig word vir plastiek, keramiek, glas, sement, rubber en farmaseutiese vervaardiging, as korrosie-reserende bevattings in die petrochemikale vervaardiging, as korrosie-reserstowwe bevat in die petro-jarige vervaardiging, en korrosie-resiers bevat in die petro-farmaseutiese vervaardiging, en korrosie-resiers bevat in die petro-jarige vervaardiging, en korrosie-resiers bevat in die petro-farmaseutiese vervaardiging.
Bestaande spesiale grafiet -silikonkarbied -smeltkroes en produksieprosesse produseer produkte met 'n gemiddelde leeftyd van 55 dae, wat te kort is. Die gebruiks- en produksiekoste neem steeds toe, en die hoeveelheid afval wat gegenereer word, is ook groot. Daarom is die ondersoek na 'n nuwe soort spesiale grafiet -silikonkarbied -smeltkroes en die produksieproses daarvan 'n dringende probleem om op te los, aangesien hierdie smeltkroes beduidende toepassings in verskillende industriële chemiese velde het.
[0004] Om bogenoemde probleme aan te spreek, word 'n metode vir die voorbereiding van hoë-sterkte grafiet-silikonkarbiedfunksies vir metaalsmelting voorsien. Produkte wat volgens hierdie metode voorberei is, is bestand teen hoë temperature en korrosie, het 'n lang lewensduur en bereik energiebesparing, emissievermindering, omgewingsbeskerming en 'n hoë herwinningsyfer van afval tydens produksie, wat die sirkulasie en die gebruik van hulpbronne maksimeer.
Die voorbereidingsmetode van hoë-sterkte grafiet-silikonkarbiedkarbied-kruisels vir metaalsmelting bevat die volgende stappe:
- Voorbereiding van grondstowwe: silikonkarbied, grafiet, klei en metaal silikon word in hul onderskeie bestanddele per kraan geplaas, en PLC -program beheer outomaties die ontlading en weeg van elke materiaal volgens die vereiste verhouding. Pneumatiese kleppe beheer die ontlading, en ten minste twee weegsensors word aan die onderkant van elke bestanddeel -hopper gestel. Nadat u geweeg het, word die materiale in 'n mengmasjien met 'n outomatiese beweegbare wa geplaas. Die aanvanklike toevoeging van silikonkarbied is 50% van die totale bedrag.
- Sekondêre vermenging: Nadat die grondstowwe in die mengmasjien gemeng is, word dit in 'n bufferhopper ontslaan, en die materiale in die bufferhopper word deur 'n emmerhysbak na die mengsel opgehef vir sekondêre vermenging. 'N Ysterverwyderingsapparaat word by die ontladingspoort van die emmerhysbak gestel, en 'n wateraanvullingstoestel is bo die menghopper gesit om water by te voeg terwyl hy roer. Die wateroptellingstempo is 10L/min.
- Materiaaldroging: Die nat materiaal na vermenging word in 'n droogtoerusting by 'n temperatuur van 120-150 ° C gedroog om vog te verwyder. Na volledige droging word die materiaal uitgehaal vir natuurlike verkoeling.
- Verplettering en sifting: Die gedroogde geklemde materiaal gaan in 'n verpletterende en siftingstoerusting om vooraf te vernietig, voer dan 'n teenaanvalbreker in vir verdere verplettering, en gaan terselfdertyd deur 'n 60-maas-siftingstoerusting. Deeltjies groter as 0,25 mm word teruggestuur vir herwinning vir verdere voorvermindering, verplettering en sifting, terwyl deeltjies kleiner as 0,25 mm na 'n hopper gestuur word.
- Sekondêre materiaalvoorbereiding: Die materiale in die ontladingshopper word teruggevoer na die bondelmasjien vir sekondêre voorbereiding. Die oorblywende 50% van die silikonkarbied word tydens die sekondêre voorbereiding bygevoeg. Die materiale na die sekondêre voorbereiding word na die mengmasjien gestuur om weer te meng.
- Sekondêre vermenging: Tydens die sekondêre mengproses word 'n spesiale oplossing met viskositeit bygevoeg tot die mengsel deur 'n spesiale oplossing met 'n spesifieke swaartekrag. Die spesiale oplossing word deur 'n weegemmer geweeg en by die mengsel gevoeg.
- Druk en vorm: die materiale na die sekondêre vermenging word na 'n isostatiese persmasjien -hopper gestuur. Na laai, verdigting, stofsuig en skoonmaak in die vorm, word die materiale in die isostatiese persmasjien gedruk.
- Sny en snoei: dit sluit in die sny van die hoogte en die snoei van die smeltkroes. Sny word deur 'n snymasjien gedoen om die smeltkroes tot die vereiste hoogte te sny, en die bars na sny word afgewerk.
- Droging: Die smeltkroes, nadat dit in stap (8) gesny en afgewerk is, word na 'n droogoond gestuur om te droog, met 'n droogtemperatuur van 120-150 ° C. Na droging word dit 1-2 uur warm gehou. Die droogoond is toegerus met 'n lugkanaalverstellingstelsel, wat bestaan uit verskeie verstelbare aluminiumplate. Hierdie verstelbare aluminiumplate is op die twee binneste van die droogoond gerangskik, met 'n lugkanaal tussen elke twee aluminiumplate. Die gaping tussen elke twee aluminiumplate word aangepas om die lugkanaal te reguleer.
- Glazing: Die glasuur word gemaak deur glasmateriaal met water te meng, insluitend bentoniet, vuurvaste klei, glaspoeier, veldspaatpoeier en natriumkarboksimetiel sellulose. Die glasuur word handmatig met 'n kwas aangebring tydens glas.
- Primêre skietery: Die smeltkroes met toegepaste glasuur word een keer in 'n oond vir 28-30 uur afgevuur. Om die doeltreffendheid van die vuur te verbeter, word 'n labirint -oondbed met 'n verseëlingseffek en lugversperring aan die onderkant van die oond gestel. Die oondbed het 'n onderste laag seëlende katoen, en bokant die verseëling katoen is daar 'n laag isolasie -baksteen, wat 'n labirint -oondbed vorm.
- Impregnasie: Die afgevuurde smeltkroes word in 'n impregnasie -tenk geplaas vir vakuum en drukimpregnering. Die impregnasie-oplossing word deur 'n verseëlde pypleiding na die impregneringstenk vervoer, en die impregneringstyd is 45-60 minute.
- Sekondêre skietery: Die geïmpregneerde smeltkroes word in 'n oond geplaas vir sekondêre skietery vir 2 uur.
- Bedekking: Die smeltkroes na sekondêre afvuur word bedek met 'n waterbasis akrielharsverf op die oppervlak.
- Afgewerkte produk: Nadat die deklaag voltooi is, word die oppervlak gedroog, en na droging word die smeltkroes verpak en geberg.
Postyd: MAR-20-2024